Sintesia's Lean Consulting Services
From production to logistics, including office operations: we offer a wide range of Lean consulting services designed to support companies through every phase of their improvement journey.
Whatever your challenge, we have the right tools to face it.
The 4 phases of Sintesia's consulting approach
Generating value, step by step
Our method unfolds in four phases, designed to guide companies toward real and sustainable change.
We work side by side with the people involved in the processes, collect data, observe daily activities, and ask focused questions. This approach allows us to deeply understand the context, identify real needs, and build trust with those who create value every day.
Listening and observation
The map provides a clear, shared overview, helping us identify areas for intervention and define improvement opportunities using a structured, visual approach.
Process mapping
Each intervention is tailor-made and aligned with available resources and business goals. We work alongside internal teams to turn strategy into tangible results, supporting managers in adopting new Lean tools and methodologies.
Action plan implementation
We monitor the most meaningful KPIs together with stakeholders and promote a culture of experimentation and ongoing dialogue.
Our goal is to make the company self-sufficient in maintaining and developing long-term results, activating a virtuous cycle of continuous improvement.
Measurement and continuous improvement
Introduction to Lean tools
Here’s a clear, concise overview of the main tools we use in our Lean consulting projects.
To learn more about a specific tool, click on it.
Value Stream Mapping
Value Stream Mapping is a strategic tool for mapping and analyzing the entire value stream, from raw materials to the delivery of the finished product or service. It allows you to visualize waste, bottlenecks, and improvement opportunities, laying the foundation for a targeted and conscious Lean transformation.
Lean Office
The Lean approach is not limited to production: offices can be optimized too. With Lean Office, we analyze informational and administrative processes to reduce downtime, bureaucracy, and duplication, improving efficiency, communication, and work quality.
Visual Management
Visual Management makes key indicators, standards, and process statuses visible and immediate. Using clear and shared visual elements, it enables people to take prompt action, improving coordination, autonomy, and real-time operational control.
Skill Matrix
The Skill Matrix is a valuable tool for assessing and developing people’s competencies. It helps manage role flexibility and coverage effectively, supporting internal growth and making the organization more adaptable and resilient.
Workload Balancing
With workload balancing, we optimize the distribution of tasks across workstations on a line or among team members, reducing waste, waiting times, and overloads. The result is a smoother flow, a fairer workload, and greater productivity.
Flow Cell
A flow cell is a production layout organization where all the activities needed to create a product are integrated into a single area, with workstations close and coordinated. This setup reduces movement, lead times, and supports continuous flow.
Makigami
Makigami is a visual tool used to analyze and simplify processes, especially informational and office-based ones, by highlighting waste, bottlenecks, and improvement opportunities.
5S
Data Visualization
Data visualization tools like Power BI turn raw numbers into clear, actionable insights. Real-time performance analysis using targeted KPIs enables faster, smarter, evidence-based decision-making.
SMED
SMED (Single-Minute Exchange of Die) is a technique that drastically reduces setup and changeover times, increasing production flexibility, equipment availability, and reducing batch sizes.
Layout design
Layout design directly impacts the efficiency of flows and workplace safety. We design functional layouts according to Lean principles, reducing unnecessary movements, improving visibility, and enhancing communication across work areas.
Kanban
The Kanban system regulates material and information flows through visual signals. It allows workstations to be replenished only when needed and in the right quantity, reducing inventory, overproduction, and management complexity.
Electronic Kanban
Electronic Kanban enhances and complements the traditional paper card system, making the pull system more traceable, responsive, and transparent. By digitizing the information flow, it synchronizes production, logistics, and suppliers in real-time, reducing lead times, inventory, and waste.
Pull supply chain
Just in Sequence
Internal Logistics
Know-how's digitalization
We guide you through your Lean journey
Lean solutions are many, and every company has different needs.
Our job is not to apply predefined solutions, but to guide you in choosing the tools best suited to your situation.
We assess the context, goals, and people involved to build a tailor-made Lean Consulting path, combining the most effective levers to generate continuous improvement and concrete results.
Want to discover which Lean tools are best for your company? Contact us!

Join those who chose to change
Not sure which service suits your needs best?
Contact us, together we’ll identify the Lean consulting service that best meets your goals.
Every meaningful change starts with a honest conversation
Tell us your challenge.
We’ll be happy to help you reach your goals.
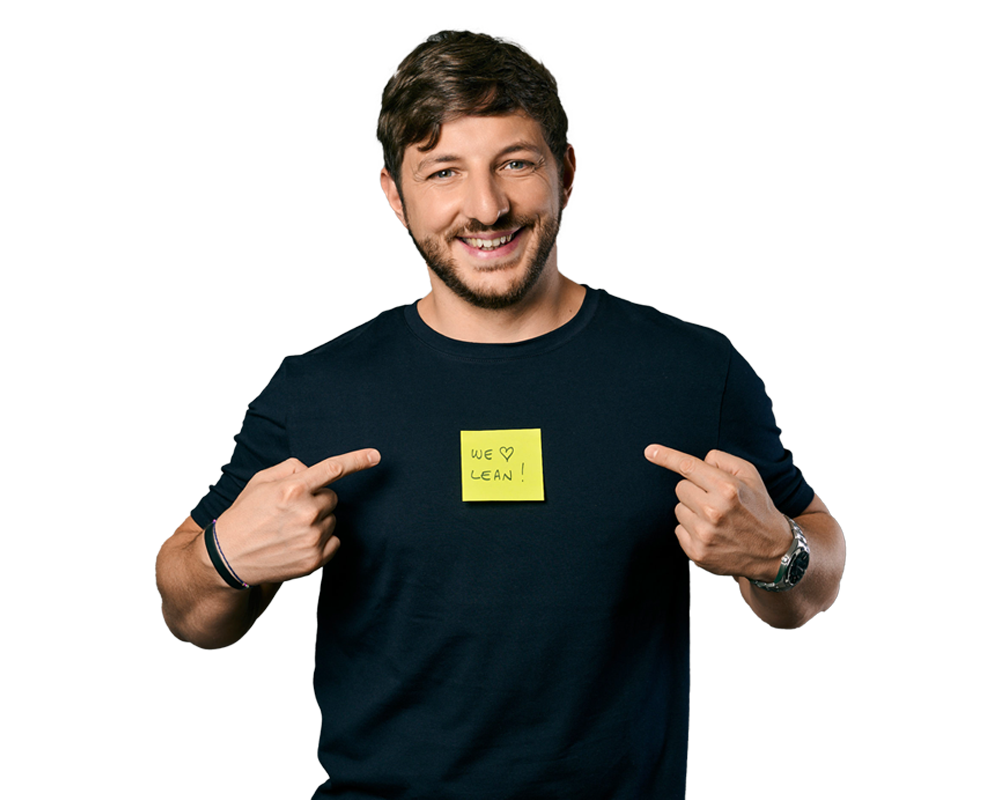